Amr Assaad of Buckley Gray Yeoman, Tyler Goodwin of developer Seaforth and Kelly Harrison of structural engineers Whitby Wood joined The Architects’ Journal at the Roca London Gallery this month to talk about how they used cross-laminated timber (CLT) in retrofit projects of their own.
The panellists agreed that CLT is in demand because of its low embodied carbon, as well as its aesthetic appeal for owners and occupiers. Many clients, said Harrison, are ‘screaming out’ for CLT to extend the life of existing buildings, lower their carbon emissions and meet EPC targets. But then they encounter some forbidding challenges with its use, including concerns about increased insurance premiums, fire safety and moisture ingress.
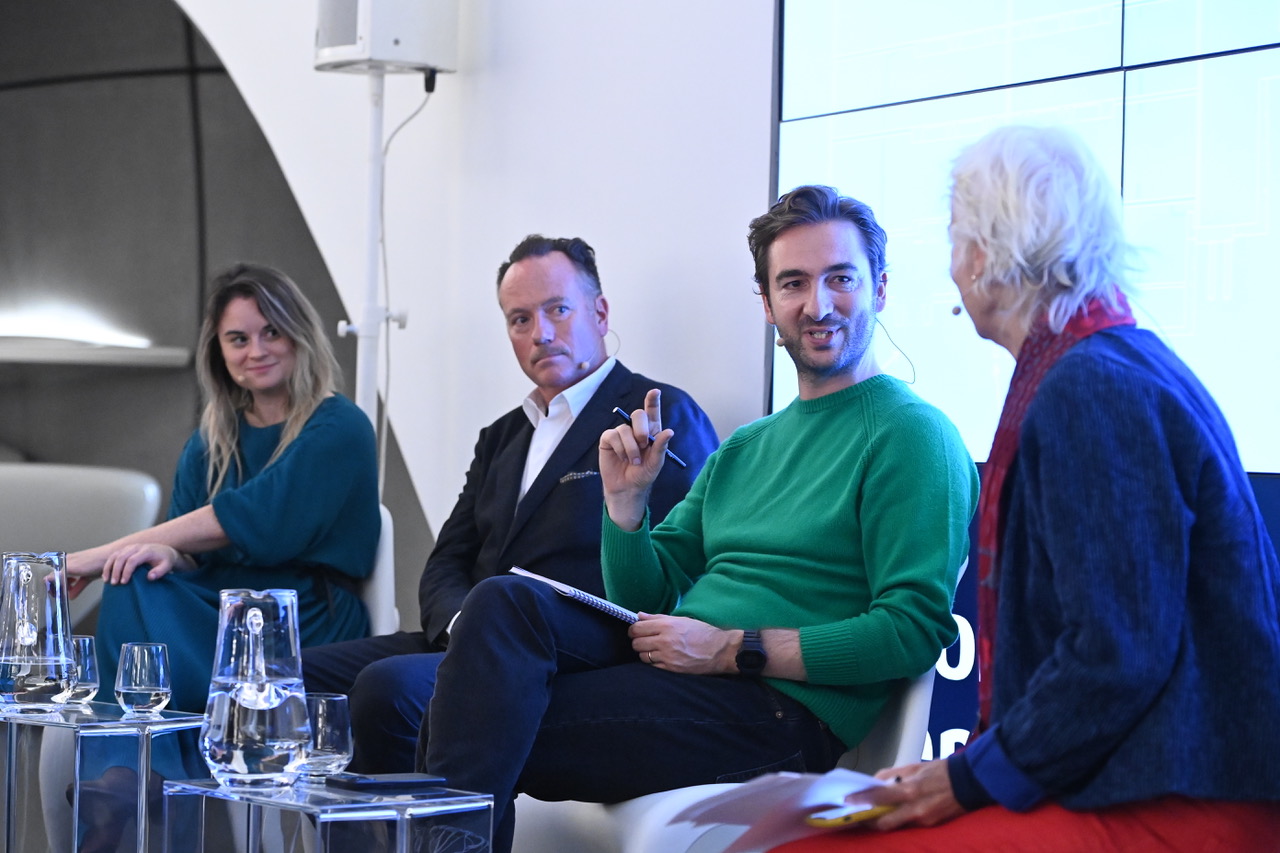
Source:Theo Wood
Kelly Harrison, Tyler Goodwin and Amr Assaad with the AJ’s Hattie Hartman at the panel discussion
The speakers said that developing a strong narrative about the benefits of CLT, and showing an understanding of the business case, would help to get more clients on board with the use of the material. They went on to talk in more detail about projects of their own.
Assaad described Buckley Gray Yeoman’s retrofit of Technique, a 1950s gin distillery in London’s Clerkenwell, to show how a CLT-led project could be sophisticated, as well as sustainable. BGY’s design team used CLT for a three-storey extension that linked two sites, saving 43 per cent in carbon emissions in comparison with steel or concrete.
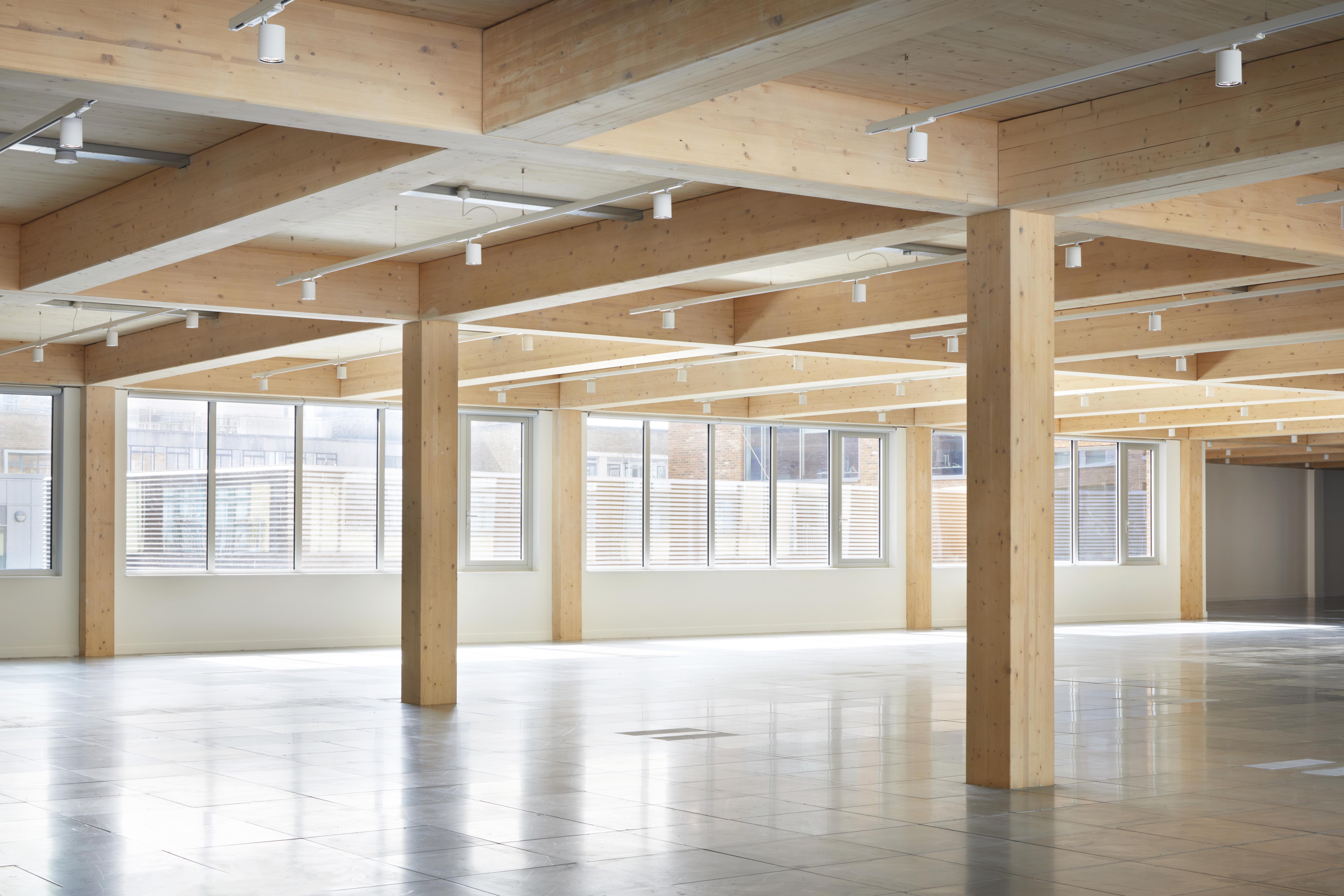
Source:Jack Hobhouse
Technique, by Buckley Gray Yeoman
Assaad said that, while people often associate timber buildings with ‘earthiness and nature’, it can be used to create something as refined as the ‘walnut finish in a Mercedes Benz’.
The upper floors of Technique’s CLT extension have already been leased, while the lower existing floors, with an exposed concrete structure, remain unlet, despite being sandblasted and carefully restored. ‘It’s amazing how quickly clients can be drawn to CLT as a construction material,’ Assaad said.
Seaforth founder and CEO Tyler Goodwin told the meeting how Groupwork + Amin Taha went about transforming the recently completed 8 Bleeding Heart Yard, an £8 million overhaul of a 1970s office block, also in Clerkenwell, for the developer.
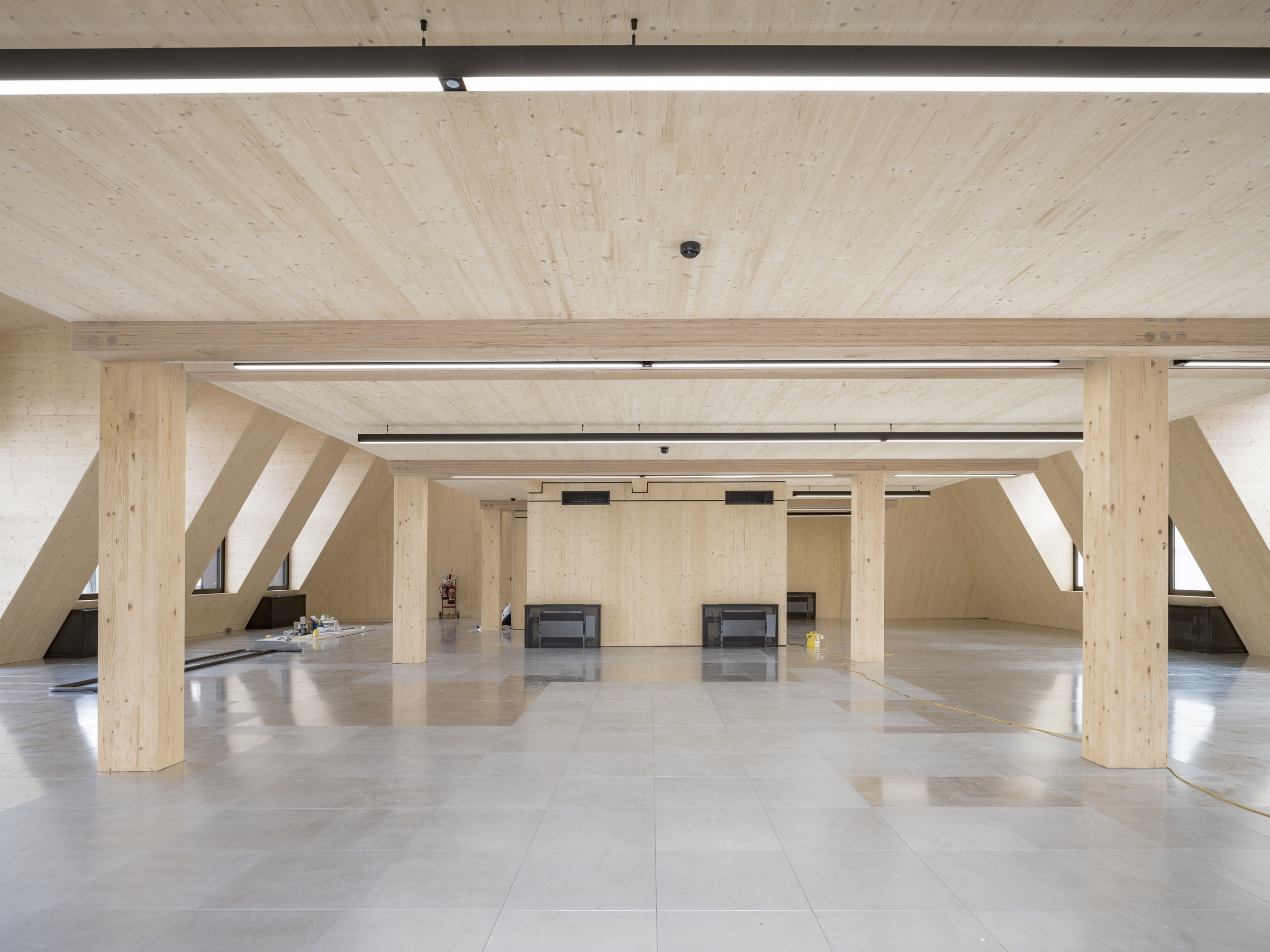
Interior, 8 Bleeding Heart Yard, by Groupwork
The scheme involved adding two CLT storeys, increasing the project’s lettable area by 50 per cent. Goodwin described how they kept the entire existing 1970s structure, insulated the exterior of the existing brick envelope and added an historically inspired external perforated metal cladding, as well as replacing windows.
‘We stripped back all of the materials. That building had an Energy Performance Certificate rating of E; it is now EPC A – something we were told would not be possible,’ Goodwin said. ‘The secret is simply stripping back all the materials on the inside. Then the outside gets highly insulated and then the façade comes on the outside of that.’
Goodwin said that, when he tours visitors through the building, ‘eight out of 10 touch the wood’.
He emphasised that architects should demonstrate an understanding of the business implications of a scheme and of using a material that could end up being more expensive up-front than steel. He urged architects to ‘take the time to run a simple real estate finance model … and speak to your client in that language’. He recalled how Groupwork principal Amin Taha had considered the return on investment of different options for the scheme.
Whitby Wood director Kelly Harrison also spoke of the need to champion timber construction, while drilling down into the challenges. Her practice has adopted the goal of becoming zero carbon by 2035 and now focuses almost entirely on retrofit projects with new-build extensions using timber or other bio-renewable materials where possible.
Encouraging clients and other project partners to buy into using CLT is challenging, owing to fear of increased costs and insurance premiums, unfamiliarity with the material, fire safety concerns and concerns about moisture ingress, she said. Contractors might also be reluctant to use CLT ‘because they like to work with their friends in the concrete and steel industry’, while fire engineers might be nervous about its use ‘because they aren’t educated in it’.
High insurance costs can present an issue with the use of CLT because insurers ‘assume a whole building will go if there’s a fire in one part’, Harrison said. But where architects can demonstrate that a fire in a CLT-structured building can be contained and the damaged part easily rebuilt because the structure is designed for disassembly, ‘premiums start coming way down’.
Moisture ingress is also an issue that architects need to think about earlier in the process when specifying CLT than with other building materials, she added, including giving adequate attention to sealing and waterproofing properly.
The speakers returned to the idea that creating a strong narrative is vital for persuading clients and tenants of the benefits of CLT. Goodwin said that seeing the emotional reaction of his tenant, Swiss private banker Julius Baer, to Bleeding Heart Yard validated the project’s design approach and suggested a strong future for increased use of CLT.
The narrative must focus both on sustainability and profitability, Goodwin emphasised. He urged architects to tell their clients: ‘It’s not just because it’s good for the environment. You can also make money from it.’
Leave a comment
or a new account to join the discussion.